

As a European fashion brand, we are committed to helping raise awareness for breast cancer and the importance of self-examination. Through various activations on C&A’s own channels as well as collaborations with influencers and women’s magazines we have been spreading the word - not only during the official Breast Cancer Awareness Month in October, but at all times.
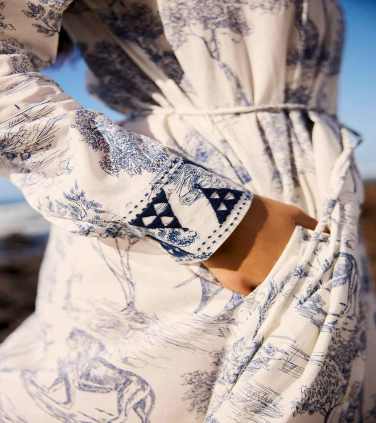
At C&A we are always exploring new ways of supporting social suppliers. Learn more about our partnership with Rangsutra, an enterprise that empowers female artisans in India. We decided to partner with Rangsutra by offering a unique Rangsutra x C&A collection of high-quality hand-embroidered pieces to our customers in-store and online to support Rangsutra in their vision of positively impacting Indian communities.
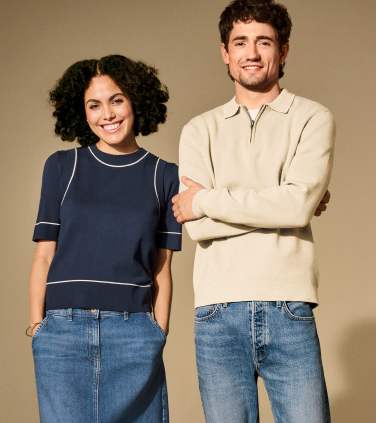
Tomorrow’s material. Everyday’s style.
In our ongoing commitment to innovation and to support a more circular fashion system, we are proud to announce the launch of a capsule collection featuring CIRCULOSE® recycled material. This advanced material will be incorporated into a variety of contemporary denim and sophisticated knitwear pieces, offering consumers a collection that harmoniously blends style with the usage of novel materials.